COMPETENCES
360° service from a single source.
We offer a 360° service based on 90 years of experience in development and production to create individual product solutions for your unique position in the market.
Development
- Application technology
- Electronics development
- Prototyping
- Software
- CAD design
- Customized HMIs
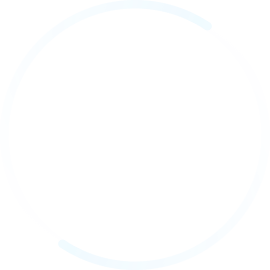
Production
- Glass processing & hardening
- Screen and digital printing
- Electronics on glass
- Optical bonding
- Assembly of components
- CNC manufacturing & engineering
Glass processing
Our portfolio of processing options for flat glass and other materials is unique worldwide.
Our stock range includes more than 250 types of glass.
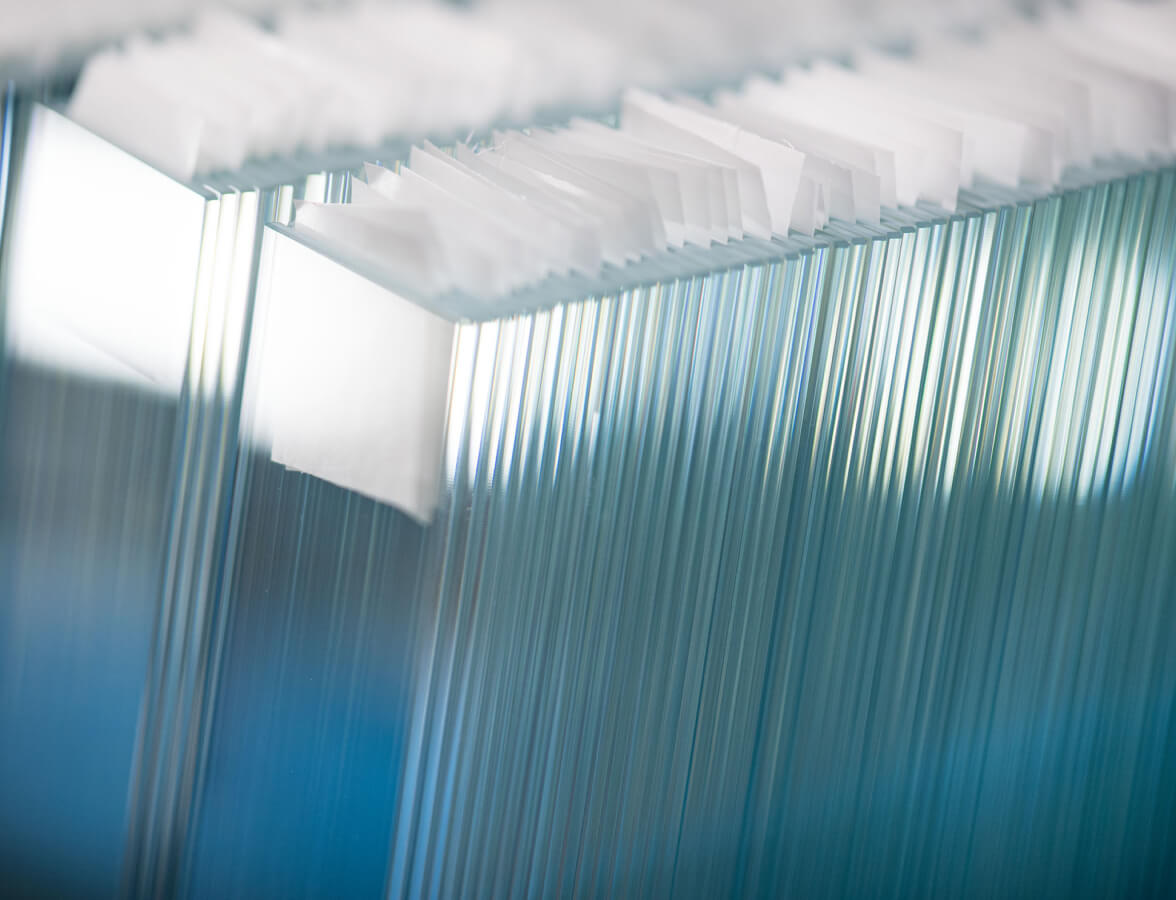
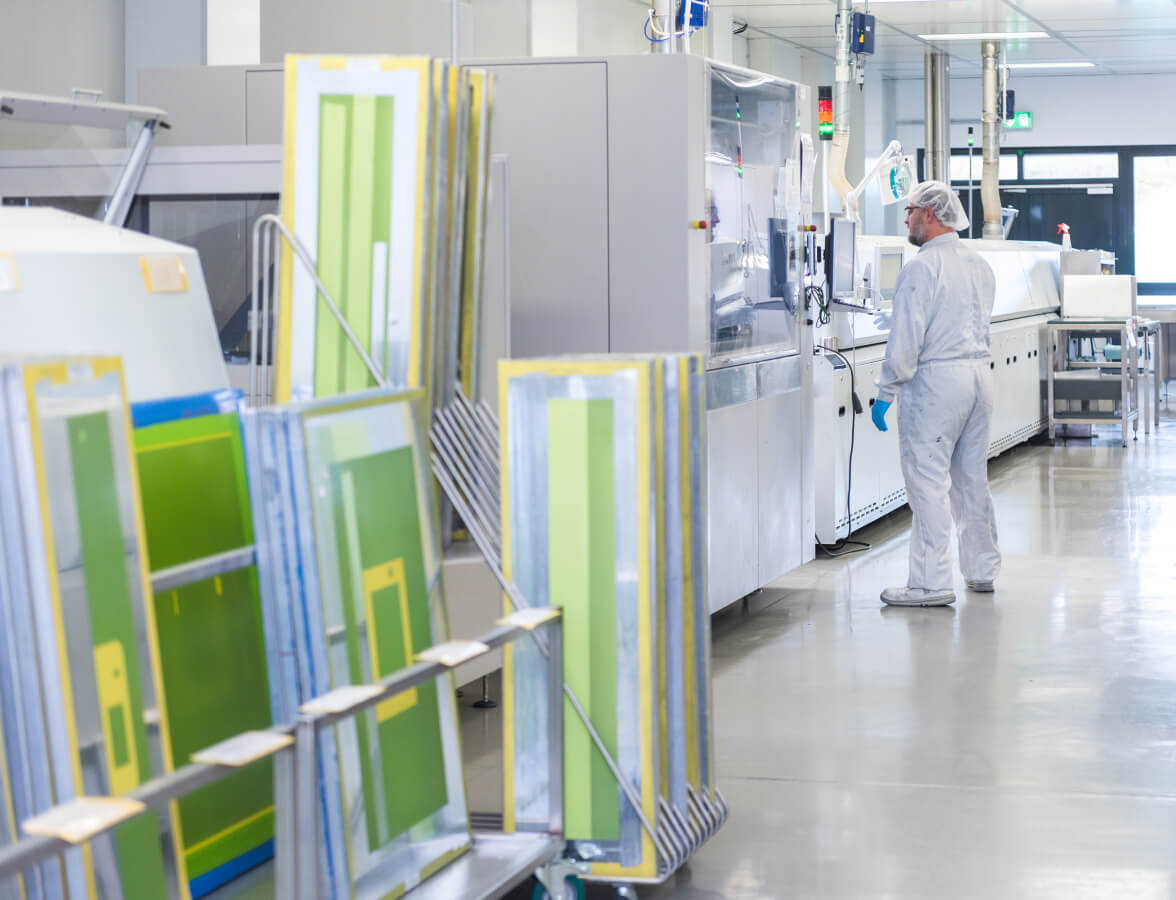
Colors and coatings
We have been able to apply colorful logos, UV-resistant designs, perfectly legible technical screen printing or electronic circuits to glass for over 30 years.
System solutions
Our expertise in developing system solutions is at its best when you challenge us with complex tasks.
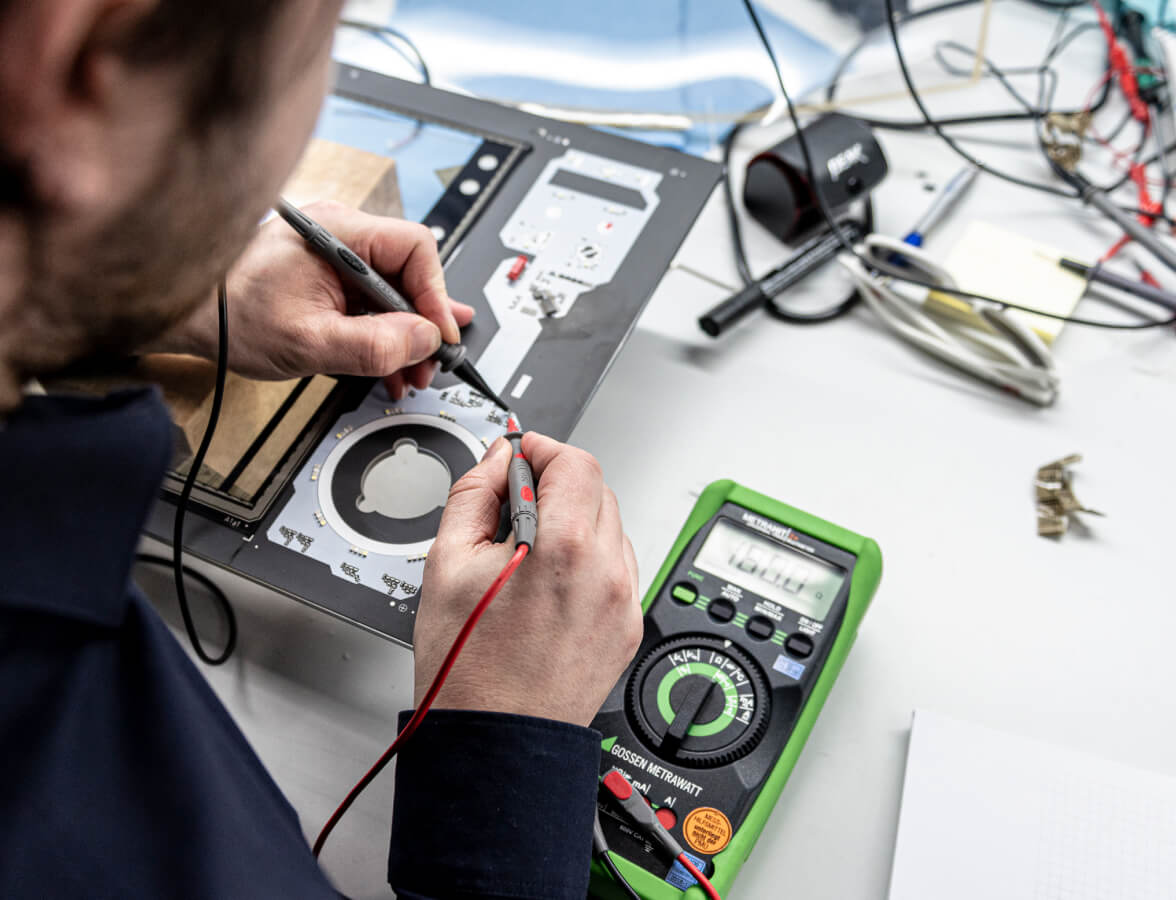
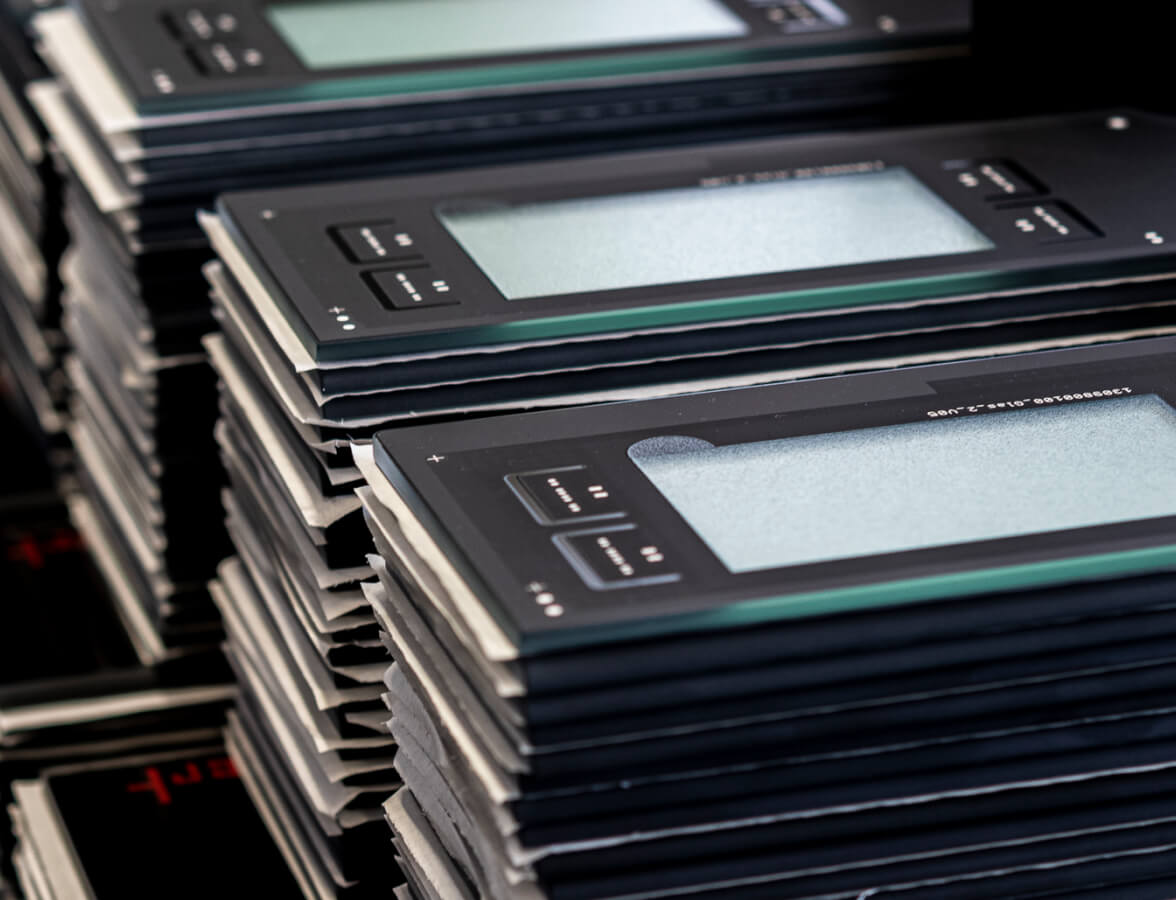
Technology platforms
Use our ready-made technology platforms for your product solution and save valuable development time.
Design & mechanical engineering
In order to meet the requirements of our customers in production, we have been developing the necessary machines and systems ourselves for decades.
